Shipment shortages, damages, and pilferage are constant, ever-present issues that negatively affect manufacturers’ bottom lines. These losses and the time-consuming process of deduction can be mitigated by taking logical steps and using deduction management software to automate the procedure.
Shortage deductions and chargebacks are usually caused by errors made by transportation carriers in shipping warehouses and at customer receiving docks. Deductions can be issued for miscounts and pilfered or missing items and can contribute to revenue losses and tedious manual paperwork processes for manufacturers and distributors.
The manual deduction management process wastes valuable manpower hours and human resources and can demand hours of time for every single claim that must be disputed. Human teams often focus on the larger deductions, leaving smaller chargebacks unattended. This results in written-off deductions and profit losses that can quickly accumulate over time.
On closer investigation, many of the shipment-related chargebacks issued will actually be overstated or completely invalid. However, without a proactive deduction management plan in place, many manufacturers and suppliers lack visibility to track shortage related claims, and instead, leave money on the table unnecessarily.
Automated deduction management software can solve this issue by addressing each claim that your business receives and automatically assessing the validity of claims to ensure that you can minimize your losses through shipment shortage deductions.
How to Prevent Shipment Shortage Deductions
1. Benchmark and compare shortage deductions.
Start by comparing shortage deduction experience ratios according to possible error sources, and track them by allocating them to each customer that charged them. Check your previous year’s statistics for your biggest customers, transportation carriers, and customer receiving centers.
2. Record your shortages.
It’s essential to keep accurate records of your shortages for all of your customers. Categorize these shortages and assign them reason codes based on whether they were listed as shipper load and count shortages, concealed shortages, or other issues.
This will enable you to pick up discrepancies between your overall shortage experience and those of your customers and allow you to recuperate deducted excesses if you have solid data to dispute chargebacks.
3. Implement shipping dock audits.
Shipping audit functions will work to prevent shipping errors and help you to identify customers and retailers that abuse your shortage claims. You can use the results of these audits to verify or dispute claims for damages, improper packaging, shortages and more.
It’s also recommended that you take certain steps to combat concealed shortage deductions. Photograph unsealed cartons, and then photograph them again once you have sealed them with printed security tape before they leave your docks. This will assist with vendor compliance claims, which could also impact your bottom lines. Make sure that your scales are properly calibrated, and take care to wrap, weigh and photograph your pallets as well.
If you receive trucker carrier claims, having packing evidence on hand acts as evidence to prove that you were not at fault, and makes the freight claims processing and payment process quicker and simpler.
4. Have shipping personnel load, count, and sign off on shipment contents as they are loaded.
Photograph the pallets as they leave the dock, and take additional photos of the loaded trailer before it leaves. You can also video-record the loading process to protect high-value shipments, especially when you have a history of shipment shortages.
5. Collaborate with your customers.
If you're fortunate to have access to a human on the retailer end, it’s important to know your customers and how they conduct business. This knowledge will reduce your chances of being issued deductions.
If you do receive shipment shortage deductions, visit the issuing customers, review their receiving protocols, and show them your statistics and audit evidence. If you have concrete evidence available, they will be more likely to improve their practices and reimburse you for the chargebacks.
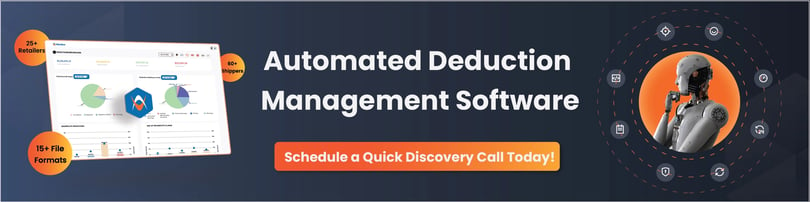
iNymbus Streamlines Root Cause Analysis
Deduction management can be a complicated, time-consuming, and expensive exercise, especially when handling shortage chargebacks. You can save your business time, money, and valuable manpower hours by using deduction management software like iNymbus DeductionsXchange to handle your process of deduction dispute.
iNymbus has been designed for all manufacturers, distributors, and suppliers who sell and ship products to over 40+ retail partners, including Walmart and Amazon. Companies that use combinations of ERP systems and internal manual processes can save hundreds of manpower hours and reduce their costs by 80% or more by centralizing all data through the DeductionsXchange dashboard.
Our solution helps you to recover lost revenues by capturing 100% of your deductions. The iNymbus system is proven to streamline and centralize all deductions and documentation, automating dispues, and helping to to preserve your profit margins as much as possible. It’s also 30x faster and more efficient than a human deduction management team, and can streamline your operations and free up labor for more pressing tasks and projects.
Streamlining Your Process of Deduction
Shipment shortage deductions are a relatively common occurrence for manufacturers and distributors. The key to addressing and resolving them successfully is using smart automated deduction management software to consistently capture shortage-related deductions and supporting documentation and consistently submitting disputes right back.
iNymbus’s robotic process automation system is capable of automatically gathering the supporting documents, numbers, and evidence you need to dispute invalid shipment shortage chargebacks without human intervention. Our specialized RPA uploads denied claim packets to retail vendor and shipper carrier portals and submits deduction disputes on your behalf. We reduce your expenses by eliminating manual labor and also allow you to take back revenue from previously undisputed and invalid shipper shortage claims.
Claim Your Free Deductions/Chargeback Audit
We also offer a free deductions and chargeback audit to identify areas of your business in which you could save money and streamline your process of deduction management. Our complimentary audits include overall ROIs for the implementation of DeductionsXchange, and are risk and obligation-free.