In retail, keeping inventory accurate and operations running smoothly is critical. For suppliers working with Walmart, shortages can be a common challenge. These happen when the number of products shipped doesn’t match what Walmart receives or records.
Handling shortages effectively is essential to keep the supply chain moving and maintain a strong relationship with Walmart. This guide explains what Walmart shortages are, why they happen, and how suppliers can deal with them successfully.
What Are Walmart Shortages?
Walmart shortages refer to instances where the retailer claims that the goods received are less than what was invoiced or expected from the supplier. These shortages can occur for various reasons and often result in financial deductions, called shortages deductions, from the supplier's payments.
Why Walmart Shortages Are a Big Problem:
Shortages can have far-reaching consequences for suppliers, impacting not only their bottom line but also their relationship with retailers. In this section, we will explore the reasons shortages are a significant concern for suppliers:
- Financial Implications: The direct impact on the supplier's revenue and profitability. Additionally creating cashflow problems.
- Volume: Shortages stand out as the most commonly occurring deductions, presenting a pervasive challenge for suppliers dealing with high transaction volumes.
See how a 2 Billion Dollar giant was troubled by a high volume of retailer deductions and how iNymbus helped them tackle this problem. Check out our latest case study!

Best Practices to Avoid Walmart Shortages:
To mitigate the risk of shortages and subsequent deductions, suppliers can adopt best practices that promote efficiency and accuracy in their operations. In this section, we will outline practical steps suppliers can take to minimize the occurrence of shortages:
- Accurate Forecasting: The importance of precise demand forecasting to prevent stock outs.
- Robust Inventory Management: Implementing effective inventory control measures to optimize stock levels.
- Clear Communication: Establishing open lines of communication with retailers to address potential issues proactively.
- Technology Integration: Leveraging advanced technology and software solutions to enhance order processing and tracking.
- Quality Control Measures: Implementing stringent quality control measures to minimize errors in production.
By incorporating these best practices, suppliers can not only reduce the likelihood of shortages but also strengthen their overall operational resilience, leading to a more fruitful partnership with retailers and a decrease in dispute-related deductions.
Most Common Walmart Shortages Codes
Code 24, Code 21, and Code 22 represent the most frequently issued Walmart shortages.
Please refer to our comprehensive article on all Walmart Deduction Codes, where we have shared essential details such as whether each code is disputable. If disputable, we also outline the necessary documents required to contest the most common Walmart deductions.
How To Dispute Shortages On APDP
The manual dispute process can be time-consuming, taking 20 to 30 minutes for a single shortage, and sometimes even days due to cross-departmental communication requirements. This becomes particularly challenging for suppliers dealing with a high volume of shortage deductions monthly, where manual handling would demand multiple full-time resources.
Below, we will walk through the complete process of disputing shortages on APDP. We have also attached pictures for each step to facilitate easy understanding.
Step 1: When on the home screen, you will observe a button to create a dispute.
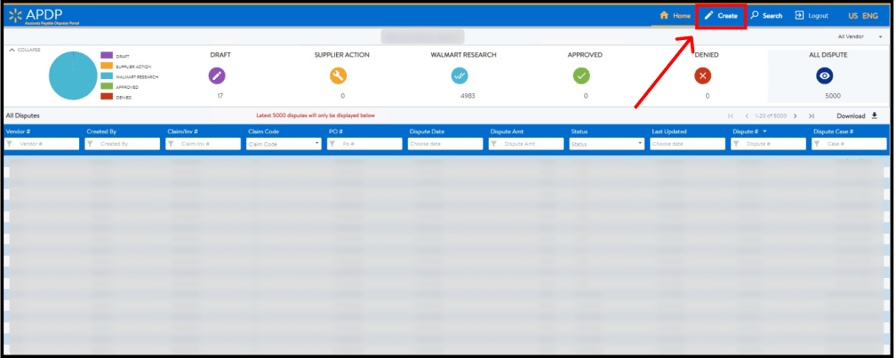
Step 2: Upon clicking that button, you will be redirected to the page depicted below. Here, you need to search for the claim or invoice you wish to dispute by entering the respective claim number or invoice number.
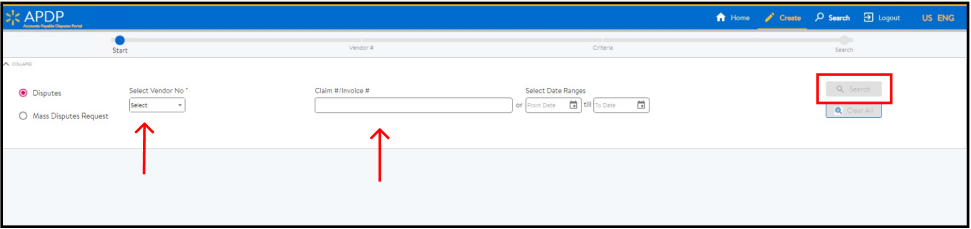
Step 3: If the information is accurate, the claim number will appear along with additional details such as the amount and claim date. Proceed by clicking the "create dispute" button.
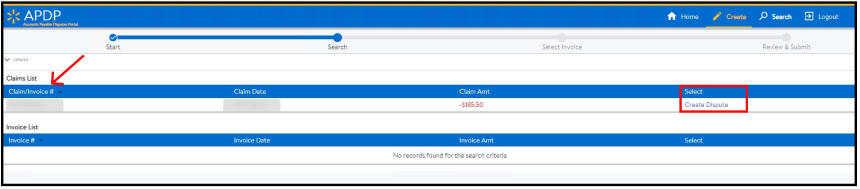
Step 4: The subsequent step involves providing a description of why the claim is deemed invalid, and you must attach documents to substantiate your argument.

Step 5: You will now review the complete claim. If everything is in order, click "Submit" to formally submit the claim.
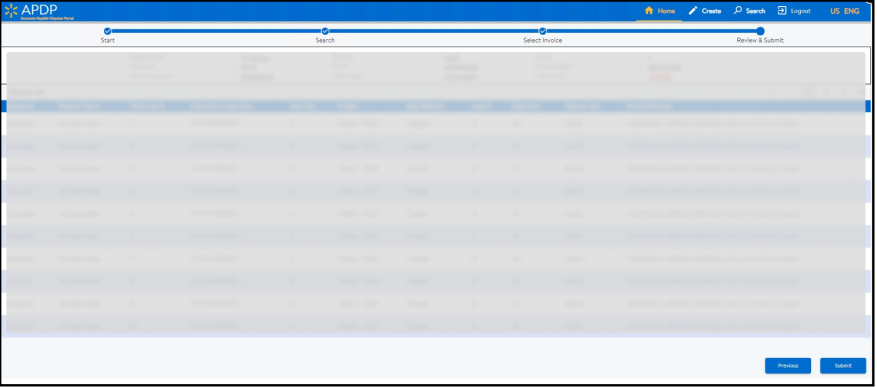
We have also written a similar article on Amazon Shortages. It has helped a lot of our readers. Check it out now!
Disputing Walmart Shortages with iNymbus
- RPA Automation for Speed: iNymbus employs Robotic Process Automation (RPA) to automate the shortage dispute process, achieving speeds up to 30 times faster than manual methods.
- Effortless Document Handling with SOPs: By establishing Standard Operating Procedures (SOPs), iNymbus minimizes manual cross-communication. The software effortlessly retrieves necessary documents from various portals and uploads them onto the shipping company's portal.
- Comprehensive Data Analysis for Root Cause Identification: iNymbus doesn't just handle disputes; it delves into data analysis to identify the origins of shortages. This proactive approach allows businesses to address underlying issues causing shortages.
- Transformation of Dispute Handling: With iNymbus, the ability to dispute shortages sees a significant transformation. What once took a day to dispute only a few Walmart shortages can now handle hundreds of disputes daily.
- Substantial Cost Reduction: iNymbus leads to an impressive 80-90% reduction in the cost per claim. The streamlined and automated process not only increases efficiency but also contributes to significant cost savings.
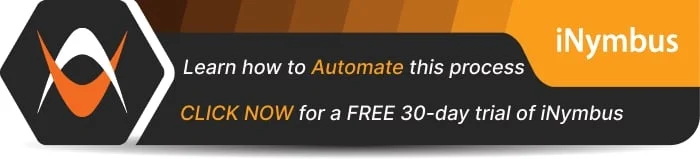